Expedition Hublot – The Fusion in Art of Fusion
A peek into the manufactures at Hublot reveals the intricacies and technology behind their often-quirky watches.
In an industry where tradition often takes more precedence over experimentation, Hublot is an outlier. They are proud of the fact their claim to fame began when they started ‘fusing’ unorthodox materials together. Over the decades, Hublot went from combining gold cases with rubber straps to fusing materials at a molecular level resulting in some never before seen within the industry. Today they are the only brand that can offer a watch case made with unscratchable gold, and ceramic and sapphire ones with colours that no other brand has managed to achieve. They are more science lab than a watch manufacture so when Hublot invited me behind the scenes to tour its facilities, how could I refuse?
ART OF FUSION REDUX
The last time I was at the doors of the Hublot manufacture in Nyon, Switzerland was in 2016. I remember it because one, it was the first manufacture I visited as a fresh-faced journalist all those years ago, and two, the building I was standing in front of, had just been inaugurated in late 2015. At the time this was a major indicator of the brand’s success. Because, consider this, it was in 2008 that the LVMH group acquired Hublot and in 2009 it opened the first building which was around 6,000sqm. Then, to need a new building, not even six years later, which, by the way, is 8,000sqm, more than doubling the size of their facilities, if that is not a sign of success, I don’t know what is.
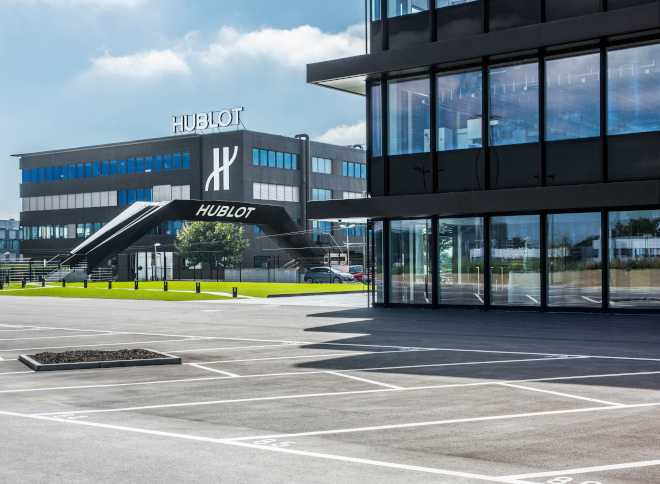
Views of the first and second building of Hublot
At the time, all of this flew over my head, but now, with a little more experience, I realised that the reason for this expansion was the Unico movement. In 2010 they made the manufacture movement, Unico, and with ‘in-house’ being the buzzword it still currently is, it was no wonder that Jean-Claude Biver wanted this expansion to focus on making these movements. I mean, the man’s foresight is practically the reason behind Hublot’s Art of Fusion, not to mention why Blancpain is still around today and why James Bond only wears Omega.
Now in 2024, Hublot have settled nicely into this new building, and as we move through the facilities for the tour, I noticed a large space being cleared right next door. You can guess what is coming next. No, it was not a new neighbour moving in, but rather once again Hublot has outgrown its current setup and is looking toward expansion. Their CEO, Ricardo Guadalupe wants to double down on in-house movements so they are building the third facility, this time with 15,000sqm of space.
This new building for Hublot will not only be focused on their in-house movements but will also bring with it an automated logistics system to transport parts within and between Hublot’s manufacture. Currently, this process is done manually where once a component is done, it is packed into boxes and transported by staff members. To make the process more efficient, an automated system with robotic elements will replace the manual parts of the logistics process. The new building is set to be complete by 2026 and when that happens, Hublot will be loaning their oldest building to the LVMH group.
WHERE THE MAGIC HAPPENS
By and large, when it comes to assembly, the Hublot manufacture is practically like every other one we have seen. Just rows of watchmakers going about their day with their loupes over their eyes, focused looks on their faces, Swiss countryside outside the window, you know the drill. Where Hublot is interesting however is seeing the various contraptions that it uses to machine and cut their cases from. And because Hublot is one of the very few brands that work with such a diverse amount of material, you can imagine the selection of machines in their manufacture.
Where most brands work with stainless steel, some precious metal and maybe titanium within their manufactures, Hublot has a selection of case materials which include the aforementioned along with some other unorthodox options like Magic Gold, the world’s only scratch-resistant gold, ceramics and sapphire. And what do all of these have in common? An extremely high level of hardness.
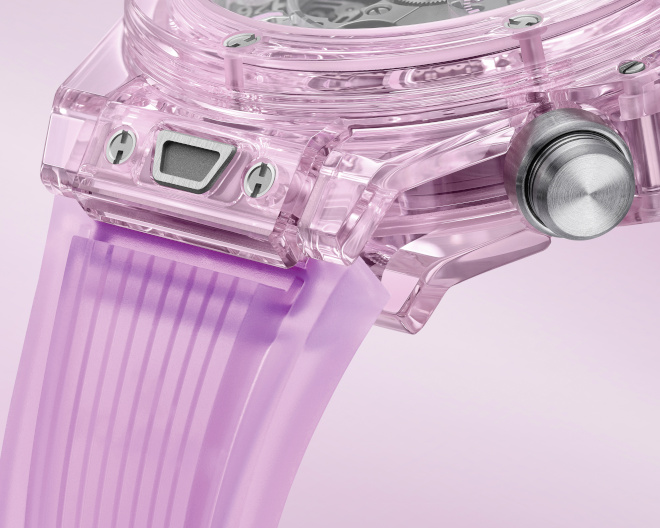
Hublot Big Bang Unico Pink Sapphire
As you would imagine, this puts an immense strain on their CNC machines which sometimes, as the Hublot representative tells me, have to work throughout the night to complete the workload. The great part of this is that the process can be automated so the employees of Hublot can still keep regular hours while the machines keep milling away. Additionally, because the range of material is so diverse, these machines are also often used to make tools for other machines, it’s all very Matrix-esque. Currently, there are roughly 25 to 30 machines within Hublot’s manufacture and each costs around about a million Swiss francs and have a lifespan of about 10 years. Apparently, it’s not just the watches that take time to make, even these machines have to be ordered sometimes a year in advance.
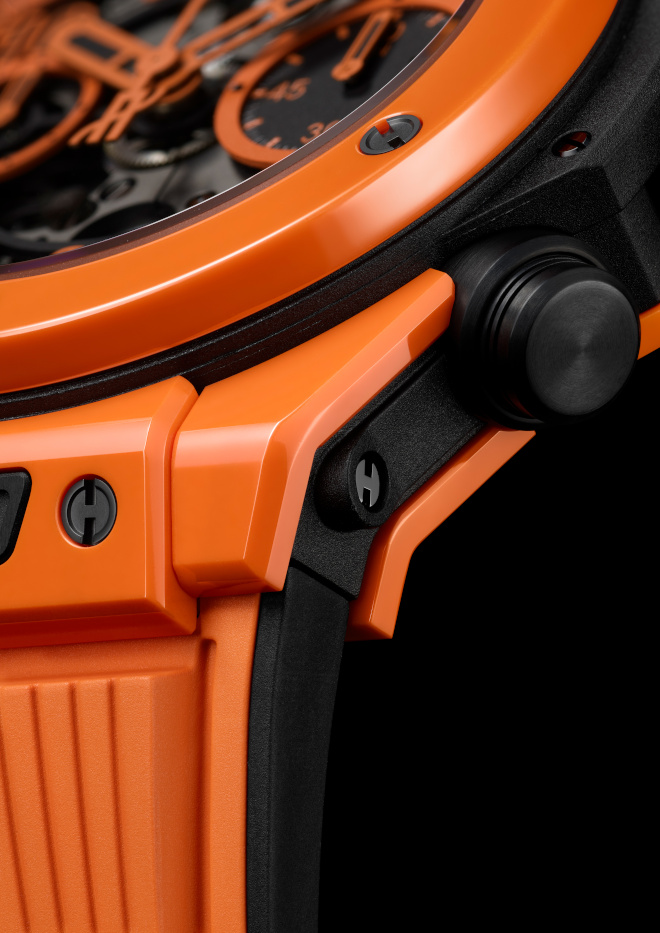
Hublot Big Bang Unico Orange Ceramic
Next, we move away from the machining of the watch components to the reason why it was imperative for them to have so many different types of machines in the first place, Hublot’s emphasis on material innovation. There is a lab within the Hublot manufacture where mad scientists dream of things like gold that cannot be scratched. With gold being one of the softer metals, to the point it normally has to be made into an alloy before it is remotely useable in jewellery or watchmaking, scratch-proof gold was at some point unthinkable. Hublot however managed this in the form of their proprietary Magic gold. And because they make this material themselves, they can explain exactly how they did it. First, they had to make a tube of boron carbide by compressing the powder at 200 bar and sintering it at about 2,700°C. The control of temperature along with the recipe of the boron carbide powder makes a material that looks smooth but is actually porous. Then, molten gold is injected at high pressures and temperatures so that it fills these minuscule holes like how a sponge soaks up water. The result is gold that is so hard that it can’t be scratched.
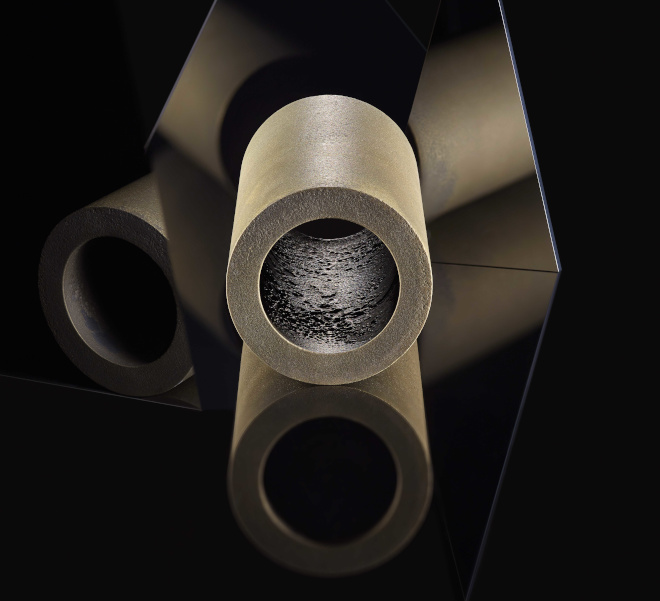
The tubes of King Gold before it is milled into Hublot’s cases
It is also in labs like this that Hublot dreams up ways to create ceramics in the most vibrant colours. Traditionally, ceramics can’t be made with these bright colours as the pigments usually burn during the sintering process resulting in dull shades. Hublot on the other hand patented a process that sinters the ceramics in higher pressures but lower temperatures so in the end the colours that emerge are still as brilliant as intended.
Up until now, Hublot is the only brand that has managed to industrialise the process of making sapphire cases. Unlike ceramics that get their colour from pigments, sapphire gets its colour through the addition of trace elements like cobalt and chromium, which are roughly the same principles that give natural diamonds and sapphires a variance in colour. In Hublot, they play god in growing and controlling the exact hue that a sapphire material is formed within their facilities. Interestingly they must make a reasonable amount of sapphire cases for them to even consider making these cases in-house. The way this is done is by heating alumina to a molten state and then introducing a ‘seed’ which is usually a piece of sapphire with the exact monocrystalline structure Hublot wants. As the molten alumina cools, the molecules will automatically mimic this monocrystalline structure giving the material its transparency. Then, tubes are cut out of these sapphire blocks before being fed to the CNC machines to get cut into Hublot’s cases.
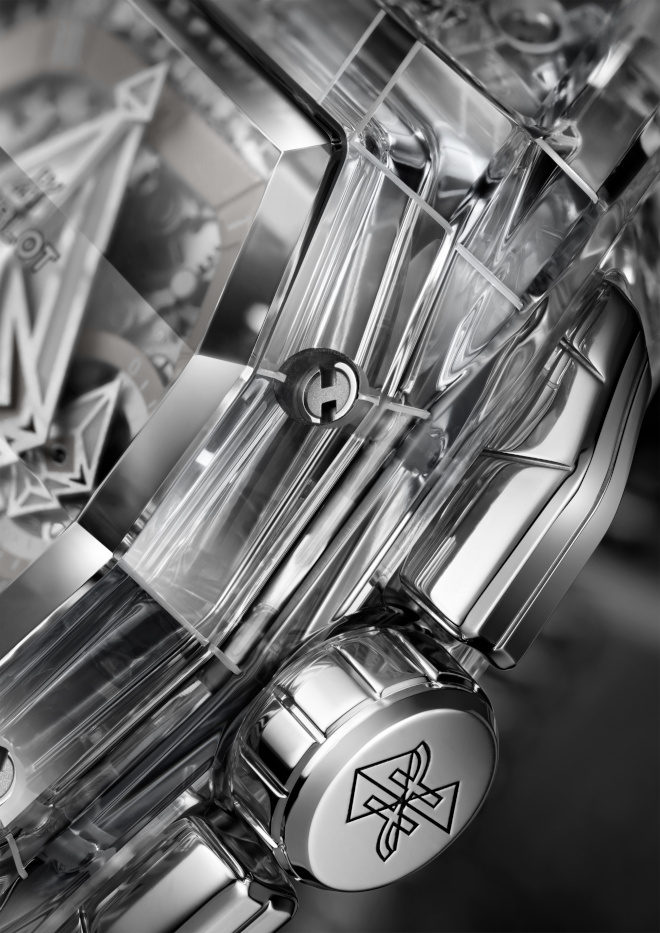
Hublot Spirit of Big Bang Sang Bleu Sapphire
Visiting the Hublot manufacture is practically part science lesson and part introduction to machining, but it did leave me with a renewed sense of awe. The brand’s flashy demeanour with its celebrity ambassadors and colourful watches may somewhat detract from the fact that Hublot really is a serious innovator in this space. Perhaps when 2026 rolls around, I will need that reminder once again and I am more than certain that the new 15,000sqm space will scarcely disappoint.