Through a cursory glance at Rado’s catalogue, it is easy to mistakenly identify it as a relatively new brand. The watches on display are mostly imbued with ceramics, giving it a glossy demeanour signalling to the customer that these are modern, high-tech watches. While the watches of Rado are modern and made through high-technology processes, you would be surprised at just how much heritage can be revealed as soon as you scratch the surface. Well, technically speaking, most of the watches at Rado are near un-scratchable but you get the meaning. Beneath the glossy, ceramic veneer, lies a brand story that spans more than a hundred years, dating back to 1917.
It is surprising, isn’t it? that the story of Rado began that long ago. Put them beside any other watch brand that has been around for the same amount of time, and it is highly likely that their watches will look worlds apart. And this is because, ever since its founding, the brand has had a fascination with innovation. Their tagline sums it up “If we can imagine it, we can make it, and if we can make it, we will!” With such unrestrained creativity, it is no surprise that most of the watches to come out of Rado defy conventional watch shapes to produce avant-garde silhouettes. However, this is not to say that in moving forward, they have discarded their history entirely. In this story, we take a look at the latest addition to the Captain Cook collection which represents a prime example of how Rado’s past continues to guide their present, or as they put it – how their heritage masters their future.
Spirit of Innovation
Although not expressly stated, we think that Rado’s philosophy regarding constant innovation is deeply rooted within its origin story. Unlike most watch brands, Rado didn’t start as a brand. It was founded as the Schlup & Co. watchmaking factory by the brothers Fritz, Ernst and Werner in 1917. In the beginning, they simply converted a part of their parent’s home in Lengnau, Switzerland into an atelier and through their industrious spirit, the trio began to grow their list of clients. By the end of the Second World War, they grew into one of the largest movement manufactures in the world. During this time, they assembled and finished watches primarily for the American market, and mostly for other brands. It wasn’t until the 1950s that they began manufacturing watches under the name Rado.
Establishing the business and growing it to the size that Rado managed, for sure required an innovative mindset. At the time, industrial processes were not as streamlined as it is today and so most likely every watch manufacture had to continuously evolve to create the most efficient processes. This mindset prevailed and when Rado started creating watches under its own brand name in the 1950s, it brought with them the same spirit of continuous improvement. A case in point is the Golden Horse collection in 1957 which brought with it a waterproof case for the first time, improving the usability of the watch. Then, in 1962 they debuted the very first Captain Cook watch which took water resistance to the next level.
It was also around this time that their search for better, more robust and scratch-resistant materials led them to hard metals like those found in the Diastar case. Their foray into the material sciences then continued to evolve throughout the 1980s and by the 1990s they arrived at what many would call, Rado’s signature element, ceramics.
Quest For Hardness
Rado’s foray and subsequent mastering of Ceramics can perhaps be attributed to the continuation of what they managed to achieve with the ultra-hard Diastar back in 1962. The impetus for this collection was to create a case that could not be scratched and today, ceramic is one of the materials that offers an even greater level of hardness. 1,250 Vickers of hardness to be precise and just as a comparison, stainless steel clocks in at about 180 Vickers.
Additionally, ceramic is also chemically inert and biocompatible, which means, the material is hypoallergenic and completely complementary to the human body. In fact, Zirconium oxide (ceramic) was once used to create the femoral cap in hip implants due to these exact properties. This biocompatibility is also perhaps one of the reasons why people often remark that ceramic feels like nothing else to the touch. It has a sort of silkiness that gives the wearer a feeling of extreme comfort on the wrist. Last but not least, ceramic also doesn’t discolour when exposed to ultraviolet light. Meaning that Rado’s ceramic watches will retain their vibrant colours throughout the watch’s entire lifetime.
With that being said, however, it is these fantastic properties of ceramic as a material that also make it incredibly difficult to work with. Especially in the watchmaking industry when production tolerances can sometimes come down to mere micrometres in deviation. Like all ceramics, zirconium oxide also begins as an ultra-fine powder and with its melting point at 2000°C special processes are needed to shape it into watch cases. You can’t melt the ceramic and pour it into moulds because most ceramics melt at temperatures higher than metal.
Achieving their title of “Master of Materials” took more than just a few years of research & development and investment from Rado. Throughout the years, they created and perfected their ceramic-making techniques. Today the Rado manufacture has machines for injection moulding, specialised formulas that can processes that produce ceramics in a wide array of colours, ovens that can sinter ceramics at extremely high temperatures over many hours, and even an oven designed to discharge gas activated by plasma at over 20,000°C.
Cooling Off
The Captain Cook collection is currently one of Rado’s most celebrated models and for good reason. It is bold and rugged, and you’d be hard-pressed to find a watch enthusiast who can pass up a great dive watch. The modern Captain Cook watches we see today were only relaunched relatively recently in 2017. Before that, the watch was discontinued and laid dormant in Rado’s archives for almost 40 years. This fantastic dive watch was first launched during the same year as the Diastar in 1962 and was created to address the growing number of recreational divers thanks to the improvements and widespread acceptance of scuba diving equipment.
As with most dive watches of the past, the Captain Cook watches also had a uni-directional rotating bezel that would help divers keep track of time during their dives. These bezels played such a pivotal role in diving that they soon became the defining characteristics of a dive watch. Of course, this design feature had to be complemented by an equally precise movement and great legibility for it to become a functional tool for divers. Then, in 1968, the Captain Cook was discontinued, and it was surprising that it took Rado nearly 50 years to resurrect this storied collection.
In 2017, inspired by the past, Captain Cook once again hoisted its sails and was re-released, this time for a different type of diver, the desk diver. Today, nearly half a century later, the role of a mechanical dive watch lies in the fulfilment of emotional appeal as opposed to functionality, as digital dive watches can simply do so much more. However, this is not to say that these dive watches are not functional. It is a testament to the luxury watch industry that even if dive watches like this Rado Captain Cook High-Tech Ceramic Skeleton will probably not be worn while diving to extreme depths, it is fully capable of doing so. It still has the unidirectional bezel, a precise mechanical movement to ensure accurate timekeeping, fantastic legibility and most importantly a water resistance of up to 300m.
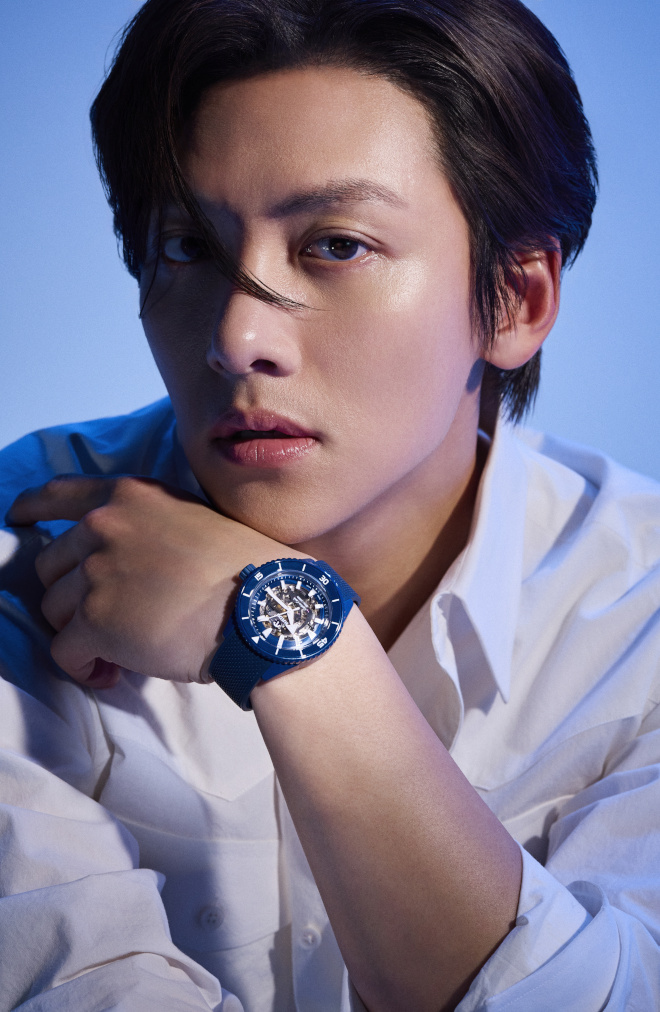
The Korean actor and singer, Ji Chang-Wook, is a brand ambassador for Rado
This watch is the perfect embodiment of how Rado uses its heritage to master its future. Because even as the watch takes its design from an intrinsic part of Rado’s history, these new Captain Cook watches have been given every update in Rado’s playbook. The most obvious of which is the high-tech ceramic case that bestows the Captain Cook with interesting colours not usually seen on dive watch cases. As with all Rado’s high-tech ceramic cases, this one also has the same scratch-proof properties which make it perfect considering the dive watch was created for more rugged use. The use of ceramic on a dive watch also provides one unexpected bonus, corrosion resistance. Saltwater is extremely harsh on materials and although stainless steel cases fare in the sea just as well, it doesn’t hurt to have this extra bit of assurance that the watch will stay as lovely as the day it came out of the box even with multiple dive excursions beneath the sea.
The first reference for Rado’s Captain Cook novelties for the year comes in a stunning version with a blue high-tech ceramic case for the first time. This blue high-tech ceramic case of the Captain Cook will also be paired with either a blue bezel for the core collection and a red or yellow bezel for the limited edition of 250 pieces worldwide. The version with the blue bezel will offer a matte blue ceramic case while the other two will come with a polished blue ceramic case. This isn’t your grandfather’s dive watch, that’s for sure. Its modern and conspicuous design language was made to suit those who like to make a statement with what they choose to put on their wrist. For instance, instead of a traditional three-link bracelet, Rado has decided to offer these watches with a more dynamic rubber strap, also in blue. And with fashion tipping towards the more casual end, the watch will most likely transition from the workday to a night out without a problem.
For those looking for a Captain Cook with a little more subtle case, there is also a version of the Captain Cook High-Tech Ceramic Skeleton that will be available in an olive green colour. This reference was inspired by the world’s cities that have become a fair bit greener as compared to before. Thus, the green chosen for the watch is in a little bit of a darker hue and is paired with an extremely elegant PVD rose-gold detailing perfect for those ‘diving’ into an urban playground. Additionally, this version of the watch will also come with the signature ceramic three-link bracelet. And as mentioned before, with comfort being one of the benefits of using ceramic materials, this is now even more apparent through the use of a ceramic bracelet as it drapes effortlessly on the wrist of the wearer.
Compounding the complexity of these Captain Cook High-Tech Ceramic models is also the skeletonised movement, the Calibre R808, fully revealed by the transparent dial. This movement is leagues beyond the calibre present in the first Captain Cook from 1962, bringing with it all the advancements in movement technology. The inclusion of a Nivachron™ hairspring within the calibre means that the watch is now resistant to magnetic fields and thanks to updates in the powertrain, the R808 is also capable of a massive 80 hours of power reserve. To ensure that the watch performs with the utmost precision, it has undergone accuracy adjustments in five different positions.